The Value of Operating Room Inventory Supply Management
The topic of operating room supply management and point of use capture in the OR continues to be an important one as healthcare organizations look to improve supply chain visibility and reduce costs. Recently, I had a good discussion with Stephanie Mittler, Senior Clinical Consultant at Mercy Hospital Washington as well as a former OR Manager for the organization. Here’s what she had to say about the impact of a clinically integrated supply chain in the OR and how it’s beneficial to the OR Manager role and to patients. (Note: her comments were written during her time as an OR Manager.)
Expiration Management
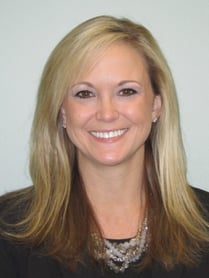
As OR Managers, we’re always working with our counterparts at other facilities to make the best use of our resources and be as efficient as we can. One way we do this is by being proactive with our expiring supplies and overall approach to operating room supply management. We look to trade them out with our other facilities that may consume them faster before the expiration date or exchange product with our company reps. I now spend only five minutes each month to ensure there is no waste in my facility due to expirations. This too adds just another safety check for our patients.
On a side note related to expiration dates, we did have a good catch shortly after rolling out the OR inventory management system. It caught an expired implant before it made it to the field. I’m confident my team would have checked the package’s inside expiration date as the item was opened, but either way, the circulator scanned the outer package as the interior package was being opened, and the point of use system flagged it as expired. BIG WIN FOR PATIENT SAFETY!
Implant Log
From an OR Manager’s perspective, consistency and accuracy are beautiful to see. For obvious reasons, the tracking of these implants is critical and prior to implementing a new supply chain system, was often a struggle for the OR team. Our accrediting/governing bodies mandate nothing but perfection in this area. Yet, with inconsistent packaging, varying lot numbers, serial numbers, manufactured-on dates, and expiration dates to consider, in the past this level of precision in documentation was inconsistent. Now everything is exactly how and where it needs to be—and better yet, it’s all traceable!
Tissue Tracking
Of course, everything I said in relation to the implant log applies here as well, but even more so. I can do an audit at any given time and drill down to the lot number of the solution used to reconstitute the tissue. I can see exactly what tissue I have on hand and follow the complete chain of custody with just the click of a mouse. My team in the room no longer has to question whether a product is considered a tissue because the application has all tissue easily identifiable and prompts for the required documentation.
One-Time Use and Trials Visibility
This report helps me manage operating room inventory from a number of different angles. It ensures accurate documentation.
Often, for various reasons, new supplies make it into our operating rooms before they are built into our system. Before, the circulator would try to find them. But if it couldn’t, they would document this in a notes section of the patient’s chart, making it untraceable (if they even charted the item(s) at all). Now, after the item is scanned just once at the point of use, the system remembers it. This ensures ease of documentation and allows our OR teams to focus on patient care.
There are also the occasional reps who like to sneak the latest and greatest products in for our physicians to try. Of course, all ORs have strict policies prohibiting this; however, without constant monitoring, this still occurred from time to time for operating room inventory. Now, with this new system, EVERY item is being scanned into our documentation. I can see exactly what “special” items are being used each day and can immediately address any issues.
Then there are the special-order items that for whatever reason we have yet to commit to inventory. This report gives me visualization into exactly how many cases this item is being used on. I can then make an informed decision on stocking the item in the future as well as the par level at which we should set.
Accurate Case Cart Content
We also completed a cleanup project with our preference cards to ensure the products contained within the cards matched each surgeon’s needs. We now have a more accurate and efficient way of managing the case cart preparation with the logistics team. This means clinical staff can spend less time searching for missing supplies and can devote more time to the patient inside the procedure room.